Forged Components
Stainless Steel Forged Components
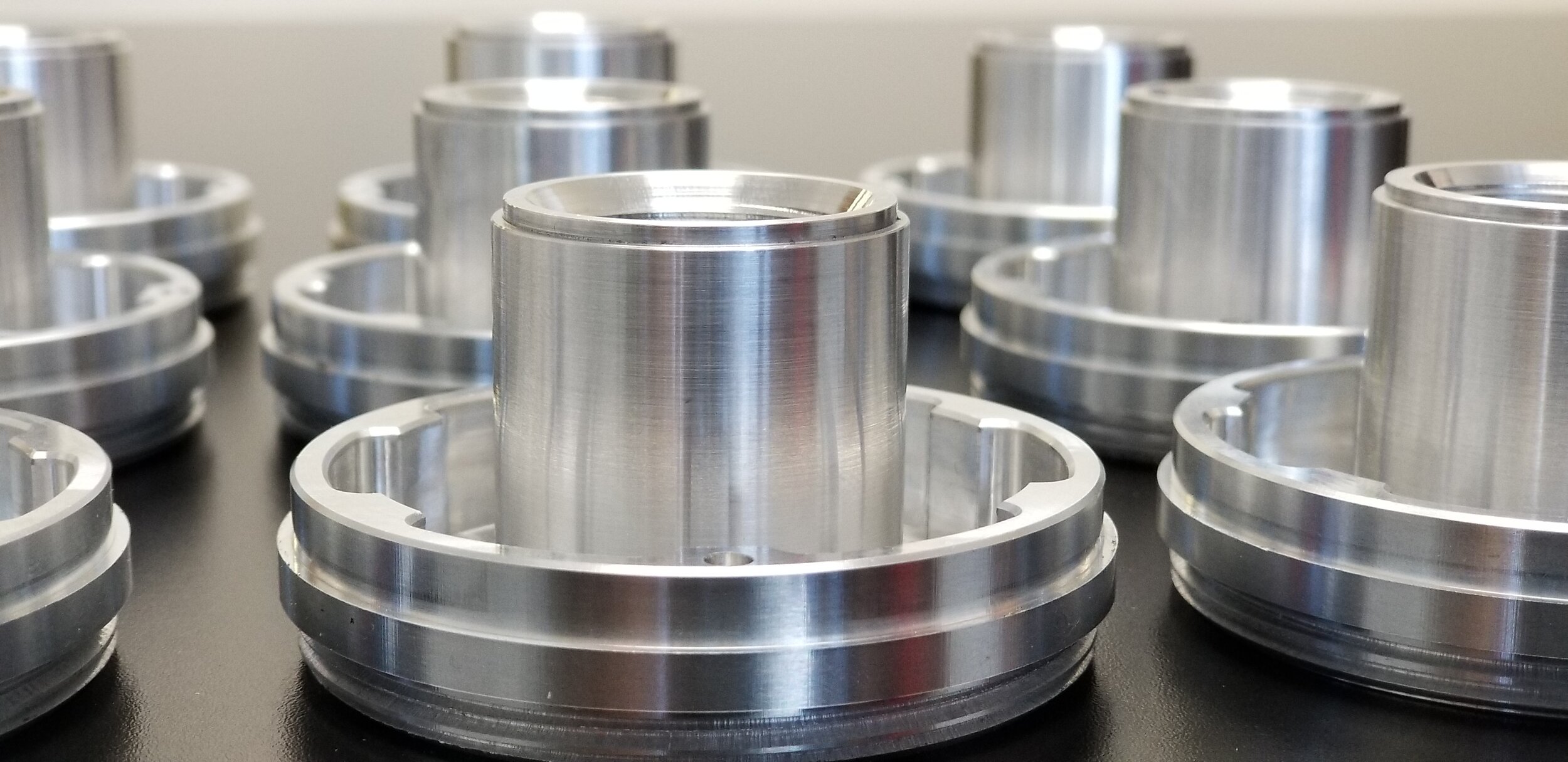
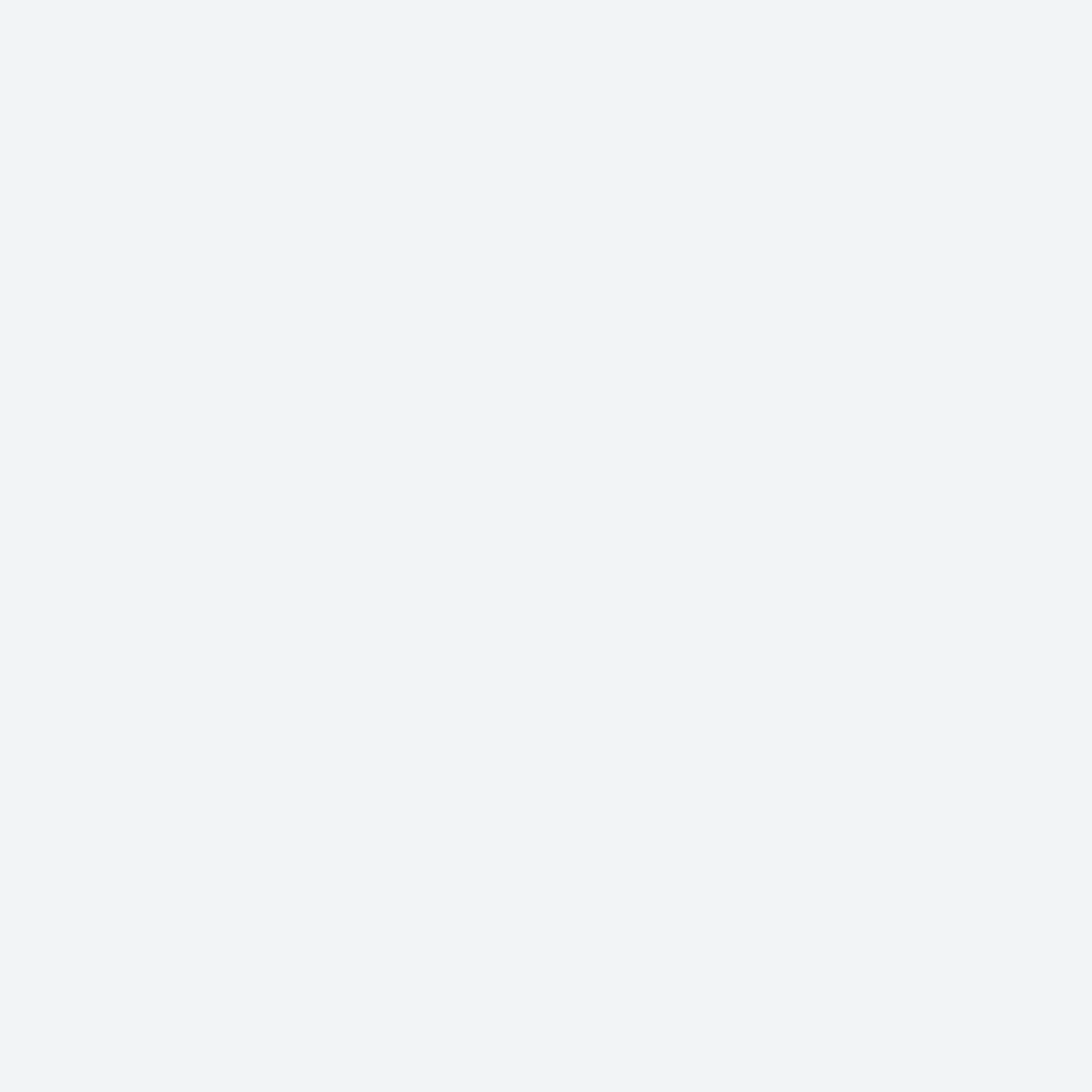
SS Forged Components
An ultimate guide about MS Forged Components
Forging is one of the most effective and oldest metalworking methods, and it is still very effective these days. In this process, metals are formed to give them a defined shape without melting them completely. To give it shape, the operator performs different forming combination techniques like pressing, rolling, and hammering by heating the raw material while it is in the solid state.
We at Imperial World Trade Pvt. Ltd. use different variations of forging, while all have their respective advantages and disadvantages. We use a high temperature to heat the material to give it a shape. Compared to other processes of metalwork like casting or any other, MS Forged Componentsbring out more physical characteristics of higher tensile strength in a very good price range.
Type of Forging
What kind of forging do we use?
The forging of the metal is defined as the deforming and forming the metal in a solid physical state. We have done the forging by the upsetting process where a ram or hammer moves upward and downward by pressing against any stem or rod to give the material shape. Before reaching the end shape, this part will go through different successive stations. We also make engine valves by using forging. We use two different forging techniques: cold forging and hot forging.
Hot forging
While doing hot forging, we heat the metal significantly, as it should be too hot before it gets hit by the hammer. The required temperature for hot forging for cu-alloys is 700 to 800 degrees Celsius. For Al-Alloys, it should be 360 to 520 degrees Celsius; steel should be up to 1150 degrees Celsius.
In hot forging, we heat the bloom or the bullet to the recrystallization point using the oven, forging, or any inductive furnace. Heating the metal is so much necessary at a highest level to avoid strain hardening for the deformation of the metal as it becomes an intricate shape in the state of plastic. The metal will remain malleable and ductile.
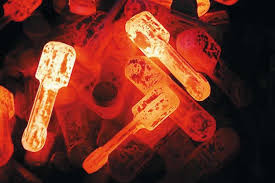
We use an isothermal forging process to forge certain superalloy metals and MS Forged Components,a very high-temperature forging process. To avoid any surface cooling, we heat the die to the temperature of the billet during the forging. We performed the forging in a controlled atmosphere to minimize the formation scale. For different kinds of fabrication, as a manufacturer, we use hot forging as it has the advantages like:
- It eliminates the porosity and chemical incongruities
- Increase the flexibility
- Homogenized structure of the grains
- Lesser work hardening and lower the risk
- Lesser work hardening and lower the risk
- Medium to low-level accuracy
- Discrete part of the production
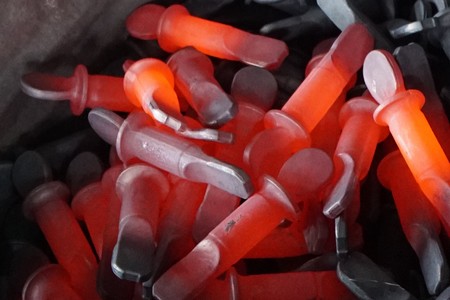
Cold forging
We generally use this cold forging to the metal while it is under its recrystallization point. We use this technique to reduce flexibility and enhance yield and tensile strength. We perform the cold forging at room temperature for metals like carbon alloys or standard steels. It is generally a closed die procedure.
We use this forging for soft metal. This cold forging is much less expensive than hot forging and requires a little finishing work at the end. To remove extra stress from the surface after cold forging, we sometimes heat-treated the metal to increase its strength of the metal.
Sometimes we choose cold forging over hot forging because it needs no or less finishing work after doing cold forging. It is also a money-saving process as it is a dispensable process. It is also not vulnerable to contamination problems, and the process outcome is better than hot forging, and we get a better finish overall. There are other advantages like:
- It gives the best outcome and net-shaped parts
- It could take high loads and high stress
- It can control the high-dimensional situation
- By this, we can enhance reproducibility
- It is easier than hot forging to impart a directional state.