Products
Forged Components
Forged Components
The ultimate guide about Automotive forged components
The manufacturing process of shaping the metals using compressing force by a hammer, basically a die or hammer, is called forging. In this process, you can have the desired shape through deforming, heating & finishing. In this process, these are classified due to the temperature in which they act in hot, warm, and cold forging.
We perform this process for producing items like kitchen warfare, jewelry, edged weapons, hand tools, and different hardware. These are commonly used in machines and mechanisms, whichever component needs more strength. Forging also needed more processing, like machining, to get the correct object. By doing heat treatment to this, you can get any shape you want.
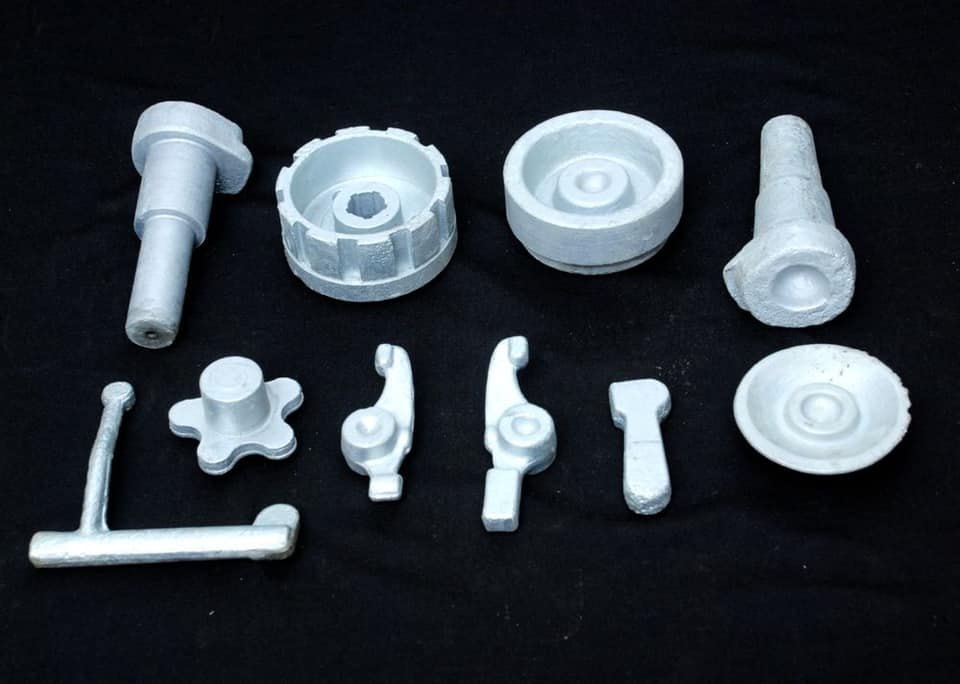
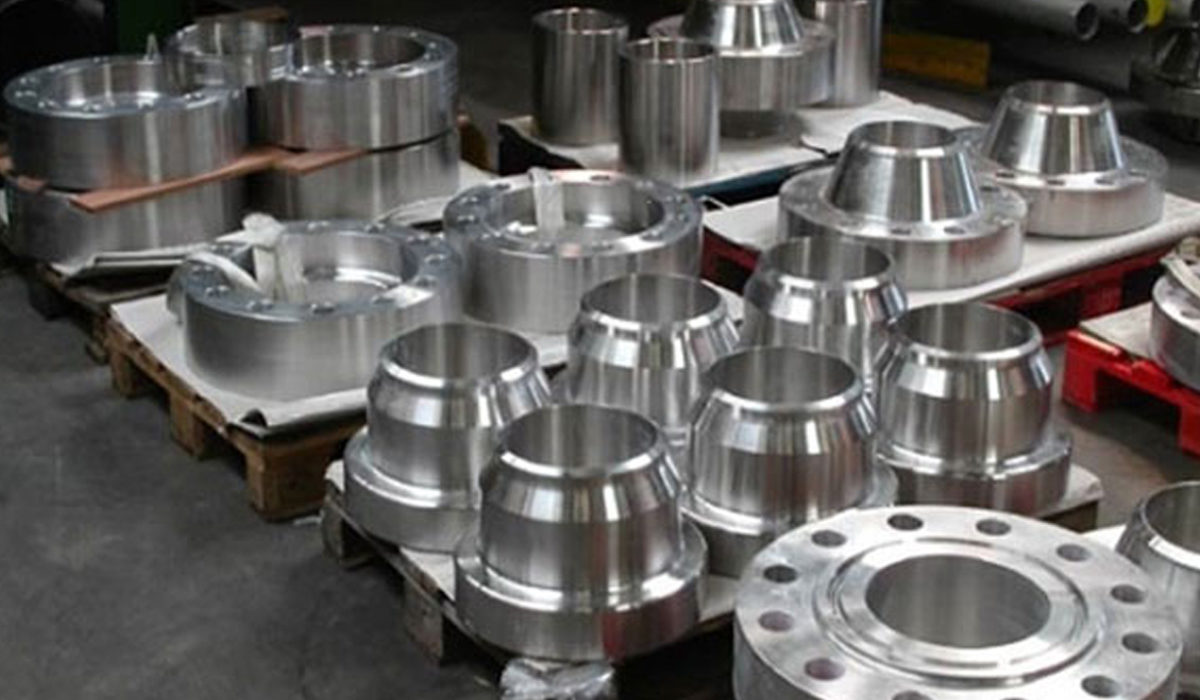
Forged Components
What is the application of our forged component?
Aerospace
The structural reliability and high weight-to-strength ratio might influence the aircraft's payload capacity, range, and performance. Manufactured from some special non-ferrous, ferrous alloy materials and forgings are commonly used in spacecraft, military aircraft, piston engine planes, helicopters, commercial jets, etc.
Some examples of forging components like arresting hooks, discs, brake carriers, wheels, struts and cylinders of landing gear, shafts, beams, brackets, engine mounts, hinges, spars and wing roots, and bulkheads, which are made due to the versatility of the forging like different properties, shape, and size. In turbine jets' engines, superalloys of cobalt base, nickel base, and iron base are automotive forged components like shafts, chambers, rings, manifolds, coupling, buckets, and blades.
Shipbuilding and ordnance
In the defense sector, from drive shafts of submarines to nuclear weapons and even rifle triggers, there is a huge implementation of forged components. There are many applications of Forged Components in the defense sector, like heavy artillery, shells, personal armed carriers, missiles, and heavy tanks.
Industrial equipment
In industrial machinery and equipment, there is a good size of forging found in the refinery industry, chemical, power transmission and generation, paper, textile, and steel. Forged configuration involves sleeves, shafts, rings, elbows, discs, cylinders, connecting rods, blocks, blanks, and bars.
Railroad/highway pieces of equipment
In handling the application of different materials, mining equipment, huge construction pieces of equipment, and off-highway construction equipment, many forging the properties like machinability, toughness, strength, and affordability. Also, for transmission and engine parts, forging is widely used for different links, bearing holders, axle beams, yokes, rollers, wheel hubs, ball joints, spindles, shafts, levers, sprockets, and different gears.
Hardware and hand tools
Traditionally forged have been the standard marks for hardware and hand tools. Some common examples are eye bolts, turnbuckles, hooks, sockets, clips for wife rope garden tools and wrenches, sleds, hammers, and pillars. Dental and surgical instruments are also frogged sometimes. For electricity transmission, some special hardware like brackets, sockets, suspension clamps, and pedestal caps are used for the resistance, dependability, strength, and corrosion resistance due to the forging.
Oil field application, Fitting, and valves
Because porosity freedom and properties of superior mechanical forgings are commonly related to the application of high-pressure work in the fitting and valve industry, heat resistance and corrosion materials are used for different kinds of fitting, saddles, elbow reducers, tees, valve stems and bodies, and flanges. Application of oil field line fits of high-pressure valves, drilling hardware, rock cutters, etc.
Sometimes non-uniform cooling and selective heating might lead to the failure of the specific area of the machine. The end product of the process will have a very good grain flow and will not have any internal voids. Unlike the casting products in our forging process decrease the occurrence of porosity and shrinkage. The chances of temperature and failure because of stress are negotiated for Forged Components.
Advantage
Advantage of using our forged components
- Our forged components are stronger than other products.
- These are very reliable products and not that much costly.
- Our products are responding better to heat treatment
- By Forging, we provide better metallurgical and more consistent properties.
- To make different types of shapes, we used forging.
- We are very flexible with the design.
- We have offered a wide range of products in different shapes and sizes.
- Making the final look of the products appealing sometimes needs a secondary operation.
Forged Components
Types of forging we do
Machine forging
The main difference between machine forging and press forging is that it becomes upset in machine forging, and in press forging, we draw out the material.
Smith forging
For making various tools like village blacksmith, we use the same smith forging. In this process of getting shaped, the heated material is continuously blown by the hammer.
Press forging
Press forging applies an external force to the material using a hydraulic machine.
Drop forging
In this operation, make a close impression with hammer drops. In many blows, force is applied to shape the material.