Products
Casting Products & Parts
Casting Products & Parts
To Make Our Work Simpler Casting Product Play An Important Role!
With an expansion in industrial markets and applications, there has been a parallel boost in demand for complex and high-quality outcomes. Fortunately, there are diverse types of casting processes that can manufacture intricate and precise products for various applications and user requirements.
The casting process is a manufacturing method that produces desired-shape metal parts by surging molten metal into a mold and congealing and cooling it to room temperature. It can produce complex and intricate parts, irrespective of their size. Casting can produce isotropic metal parts in large and bulk quantities. As a result, makes it suitable for mass production. Furthermore, to meet specific user necessities, different types of casting differ by the material and mold used. It is beneficial to realize the advantages of these methods to select the suitable casting process for your manufacturing requirements.
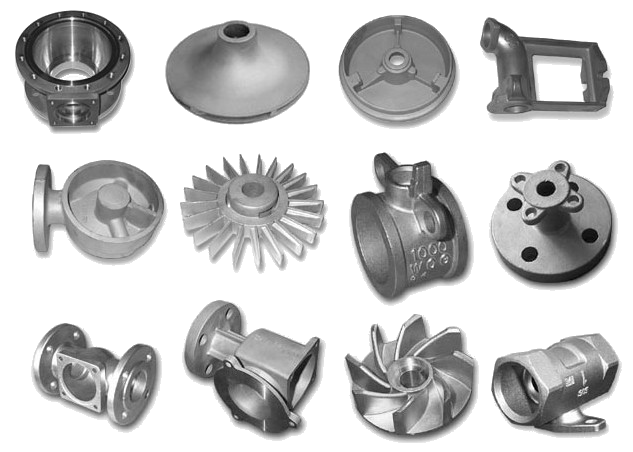
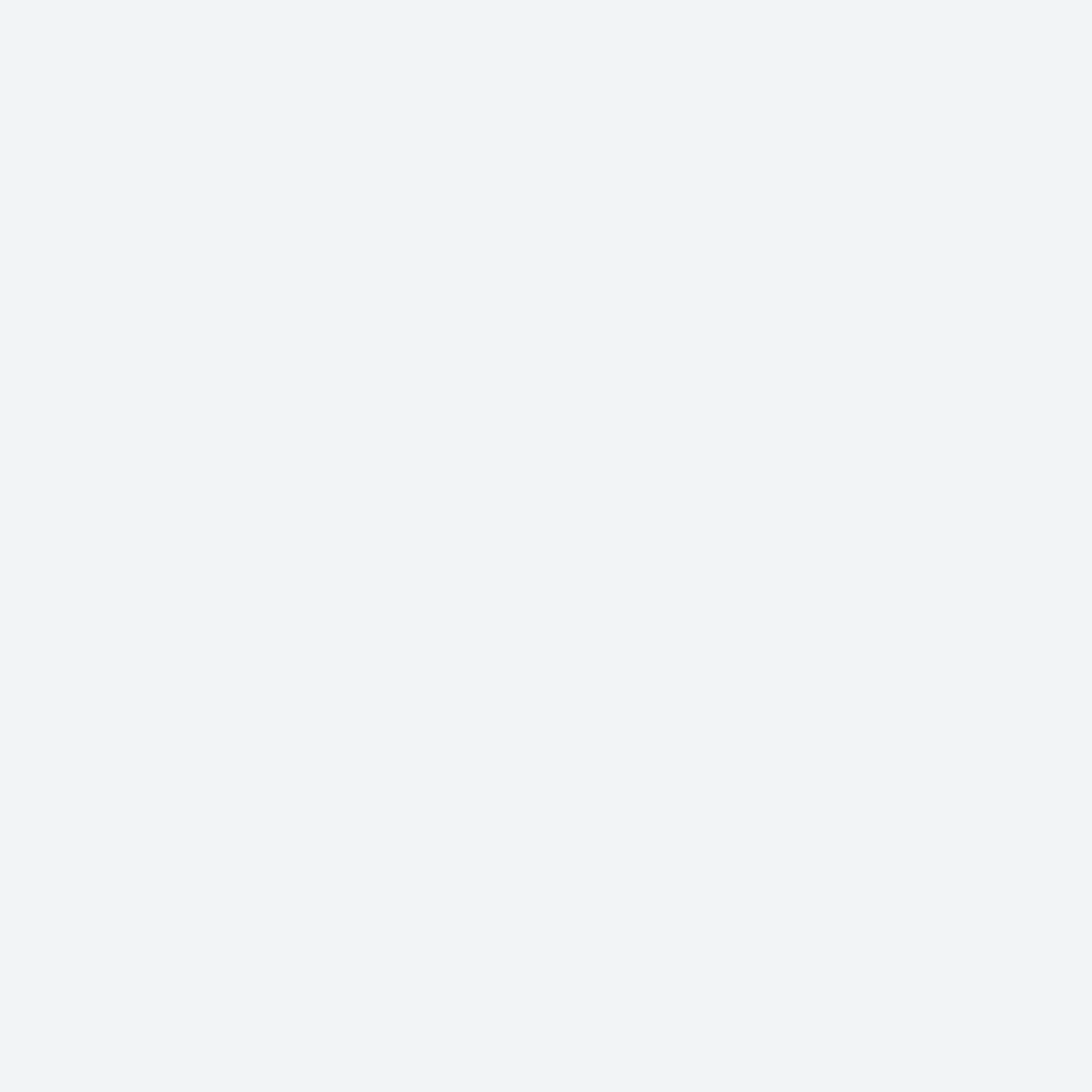
Casting Components
Investment Casting
Investment casting is one of the most cultured casting processes, encouraging intricate shapes while maintaining heightened dimensional precision and surface quality. Investment casting can cast almost any metal, fulfilling application requirements in myriad end markets. It is also known as precision casting or lost wax casting. Investment casting is usually used to build parts in convoluted shapes with high precision and surface requirement.
Advantages Of Investment Casting
Tight Tolerances
High-Quality
Complex Shapes
Application
The investment casting parts can be used for application in the following spheres:-
- automobile industries
- aero engines and aircraft
- agriculture industries
- valves and fittings
- jewelry industries
Casting Components
Die Casting
The die-casting process applies to inject molten metal with low melting points, such as zinc and aluminum, into the die-casting mold, permitting it to cool. Relying on the melting point, it emerges under two different hot and cold chamber casting mechanisms. It is appropriate for making die-casting products with simple and complex sheet metal parts. The process has a unique approach and is reliable for manufacturing many metal parts in consumer and industrial products.
Advantages Of Die Casting
Stability And Accuracy
Mass Production
Strength
Application
The die-casting parts can be used for application in the following spheres:-
- Manufacturing of consumer and industrial products
- Manufacturing of aerospace
- Manufacturing of automotive products
Casting Components
Sand Casting
Sand casting, also called sand mold casting, is a popular alternative to die-cast and investment casting. Sand casting offers advantages like a low-volume manufacturing process that is not possible by other casting techniques. This metal casting process is performed when molten metal is poured into a sand-molded cavity. Companies can save high tooling costs when sand is used as a tooling method. Typically depends on silica-based materials. Casting sand consists of finely ground, spherical grains that can be tightly packed together into a molding surface
Advantages Of Sand Casting
Low Tooling Cost
Less Time
Suitable For Low Quantities
Application
The sand-casting parts can be used for application in the following spheres:-
- Manufacturing mining machine parts
- Printing press
- Manufacturing of automotive products
Conclusion
Imperial World Trade Pvt. Ltd has various differentiated casting products to help you in your casting process; we are the leading exporter and manufacturer of industrial goods and have wide knowledge to help you to meet your needs. Get connected to us to avail the best product and services at affordable rates.